Regulatory authorities around the world conduct pharmacovigilance (PV) inspections to verify that marketing authorization holders (MAHs) and allied organizations maintain compliance with PV requirements, obligations, and relevant standards. This applies to products as well as processes. National competent authorities appoint inspectors to conduct these inspections which can be announced or unannounced. If the former, then the Pharmacovigilance inspections schedule is communicated by the Regulatory authorities in advance to the MAHs and associated organizations.
PV inspections aim to not only make sure that the MAHs’ systems, facilities, and processes are compliant with PV requirements but also to identify and record situations of non-compliance that could lead to patient harm. If these situations are identified, then corrective activities must be implemented to address these scenarios of non-compliance.
Examples of Regulatory bodies that conduct Pharmacovigilance inspections :
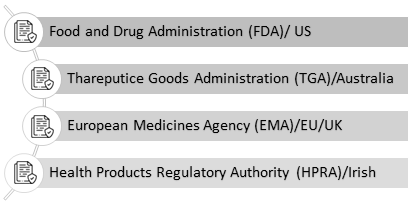
Type of Pharmacovigilance inspections:
- Pharmacovigilance system inspections
- Product-related pharmacovigilance inspections services
- Routine inspections
- For cause inspections
- Pre-authorization inspections
- Announced and unannounced inspections
- The pharmacovigilance system and related quality management systems
- Training Record and Data Archival
- Handling of adverse reaction reports (ICSRs)
- Preparation of periodic safety update reports (PSURs) and adherence to risk management plans (RMPs)
- Handling of information on adverse reactions from intervention and non-interventional trials (if relevant)
- Signal detection and risk management.
- Archival and electronic signature implementation
- Whether there are appropriate safety agreements in place and being adhered to with any 3rd party that is contracted to perform pharmacovigilance activities on behalf of the organization
- Safety data security and back-up management
- Database validation
- Ensuring technical agreements are signed, archived, and in place
- Updating the training records on Standard Operating Procedures (SOPs)
- Archiving documents as necessary
- Checking the PV Quality systems per quality management system (QMS) standards
- Collating Audit related documentation
- Providing comprehensive support, in and out, during or before the Audit or inspection
- Support of Corrective And Preventative Actions (CAPA) and Audit Report
GVP inspections: These inspections were requested by CHMP to verify the compliance, and this would be site-specific. The scope of inspection would be electronic document verification, SOP, organization chart and the pharmacovigilance system master file (PSMF).
- To assure availability of safe and effective drugs to people
- To monitor the quality of post-marketing safety data submitted to Regulatory authorities
- To help officers within regulatory authorities by ensuring the receipt of effective safety data for proper evaluation of product safety
- To evaluate the industry’s compliance with respect to Post Marketing Adverse Drug Experience (PADE) reporting requirements.
- Risk-based inspection
- The complexity of the pharmacovigilance system
- The complexity and size of the organizations involved in the pharmacovigilance system
- The compliance and inspection history of an organization
- PADE
- Risk Evaluation and Mitigation Strategies (REMS)
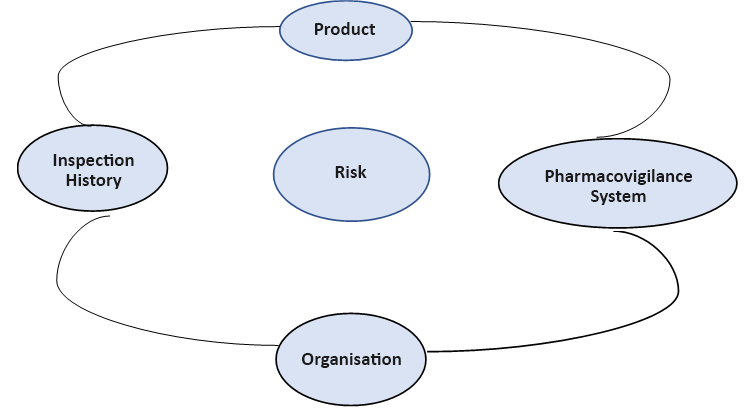
USFDA | |
Organization charts | Organogram from top-level management to the lower one involved in the PVG system |
Process/Workflow diagram | These diagrams should include various processes followed for receipt, assessment, compilation and reporting of safety data. |
Internal and external audit program | The inspector may check the audit schedule and findings from previous PVG audits. |
Training program including curriculum vitae (CV), job description (JD) and certificates | There should be easy access for inspectors to training records, CVs and JDs, which are required to provide evidence of the experience, responsibilities and training of personnel involved in safety data monitoring. |
Literature Screening | The authority can evaluate the firm process of scientific literature review for PADE reporting and whether the same has been conducted and reviewed appropriately. |
Safety Data Exchange Agreements (SDEAs) | If the MAH shares any PADE reporting responsibilities with contractors in reference to co-marketing or co-licensing of products, then USFDA can review SDEAs. |
MHRA | |
Routine pharmacovigilance activities | Routine pharmacovigilance activities -Collection and collation of safety data -Management of ICSRs (post-authorization spontaneous and solicited sources) -Periodic safety update reports –Signal management and reporting of important identified risks -Compliance management by the MAH (e.g. QPPV supervision, performance monitoring, audit) |
Routine risk management and safety communication | To assess whether important safety updates have been communicated to patients and healthcare professionals in the UK, either through the authorized product information, direct healthcare professional communication (DHPC) or educational materials. |
Additional risk minimization measures (aRMMs) | To assess whether aRMMs are being implemented in accordance with the agreed risk management plan (RMP). |
Non-interventional post authorization safety studies Non-interventional post authorization safety studies (NI-PASS) | To assess whether PASS are being conducted in accordance with the approved study protocol and that safety data is collected and reported appropriately. |
- The MAH lacked documentation for the implementation of additional risk minimization measures (aRMMs) and adequate oversight and monitoring by the EU QPPV of the adherence to risk management plan (RMP) commitments.
- There were failures in the implementation of an electronic risk management system linked to a condition of specific marketing authorizations. These failures meant that reports submitted to the MHRA on the effectiveness of and adherence to additional risk minimization measures were inaccurate.
- The Pharmacovigilance inspections reported widespread failures in the delivery of pharmacovigilance across critical pharmacovigilance processes.
- The MAH had failed to ensure appropriate oversight of the pharmacovigilance system. The system was not fully represented in the pharmacovigilance system master file (PSMF) and this had an impact on the planning and conduct of the inspection.
- The failure to deliver compliant activity across a number of critical pharmacovigilance processes, and in the context of the deficiencies being known to the MAH, was a serious breach of legislation.
- The MAH did not have the appropriate mechanisms and systems in place to allow for adequate ongoing safety monitoring, including signal detection.
- There were examples of safety signals that had been identified by a previous pharmacovigilance service provider but had not been further evaluated, and there was a failure to maintain records of ongoing safety monitoring activities conducted by the previous service provider.
- The MAH had also failed to submit a safety variation application by the deadline following a published PRAC recommendation.
FDA’s Post marketing Adverse Drug Experience (PADE) Compliance Program monitors industry compliance with post marketing laws and regulations for products regulated by the Center for Drug Evaluation and Research (CDER) to ensure that accurate, reliable, and timely safety data is submitted to FDA and available to reviewers who use this data to evaluate product safety.
- Investigations and CAPA
- Data Integrity Issues & Impact
- SOP Procedure and Practices
- Managing MA documentation and keeping it up to date.
- Tracking the implementation of variations and regulatory commitments.
- Responding to requests from Competent Authorities to vary MAs (e.g. SPC and PLs).
- Audits of the activities and QMS of the MAH are important.
- Self-Inspection, enhance training and development program.
Implementation/overcome challenges of Pharmacovigilance inspections :
Review the MAH established organizational structure to confirm that it includes provisions for responsibilities, authorities, and necessary resources.